Taking a Different Tack to Mechanical Stress
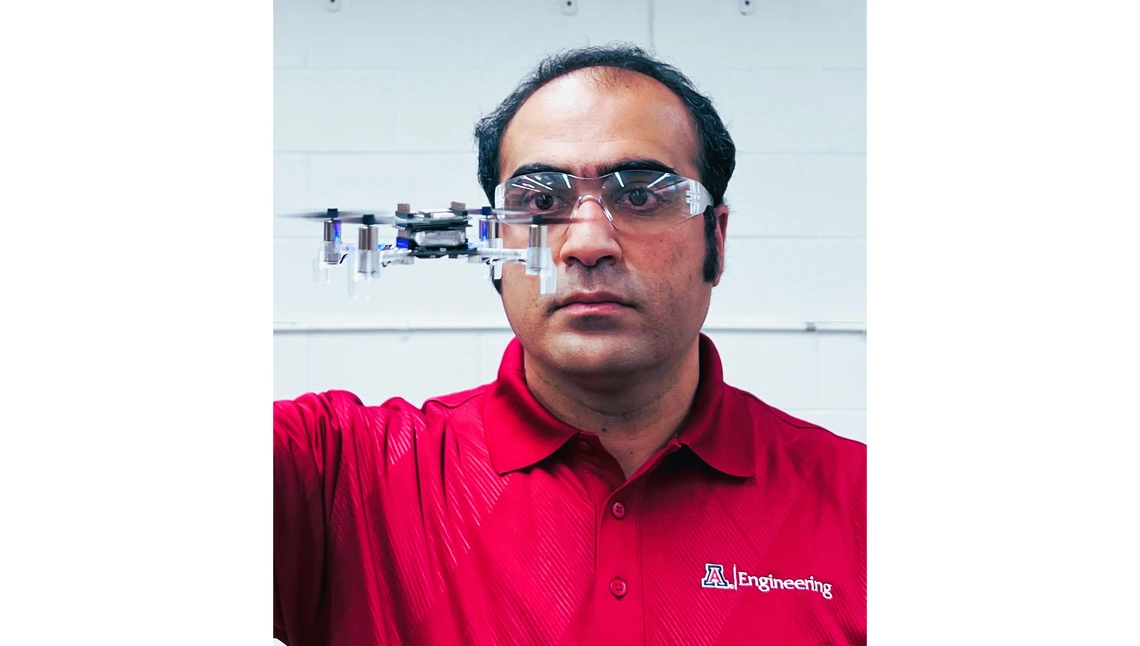
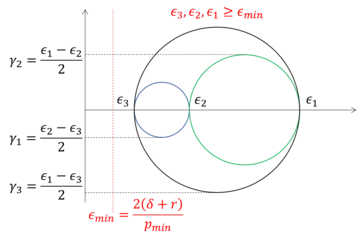
One of the most fundamental concepts engineering students learn about in their undergraduate careers is the mechanics of materials. In this field, engineers study how structures or other deformable bodies are affected by stresses and strains. For example, they learn about how much weight a beam can bear before it starts to deform, and how that deformation will look. Or they’ll examine how altering the material, size or shape of a structure changes the way it is affected by stress. This forms an important base of knowledge for fields ranging from aircraft design to building construction to marine engineering.
Computer models and Mohr’s circle diagrams are used to depict conceptually how a surface is affected by stress. But these methods for teaching students, and even doing research, have their limitations.
“Existing computer models show the effects of strain using colored contours, but they can’t visually convey distance,” said Hossein Rastgoftar, an assistant professor of aerospace and mechanical engineering and electrical and computer engineering. “So far, material deformation and strain have only been analyzed using theoretical and numerical approaches, then experimentally validated with expensive machines and tools.”
Rastgoftar and AME graduate student Harshvardhan Uppaluru have come up with an unconventional way of conveying these concepts to students: a network of quadcopter drones.

“We’re proposing a new approach for visualizing stress and strain,” Rastgoftar said. “The idea is that we treat the quadcopters as particles of a deformable body, so the concept of strain is shown by the changing distances between the quadcopters.”
Users set up an array of drones that represent the individual particles of a deformable body – say, for instance, a beam on a bridge. Then, they use a GPS command to simulate applying strain to this 3D model.
“We use a miniature local-GPS system to locate and advance the quadcopters to desired positions,” said Uppaluru. “We currently use six to eight quadcopters, but we can extend it to any number.”
To simulate downward pressure on the center of the beam, for example, the middle drones might go down while the ones on the sides move up – showing the way a beam would curve into a U shape under a heavy weight. This is a simplistic example, but the method can be used to visually display much more complex combinations of stress and strain.
“By introducing new roles for drones as ‘teachers,’ this work could provide an opportunity to practice the theoretical concepts of mechanics in an easily understandable way,” Rastgoftar said.
Rastgoftar hopes to incorporate the method in a new undergraduate elective course for aerospace and mechanical engineering. He also envisions researchers using the method to test aggressive forms of deformation more affordably. In fact, the team has a fleet of 50 lightweight quadcopters ready for large-scale experiments.
A preprint of a paper about this work is available at arXiv.
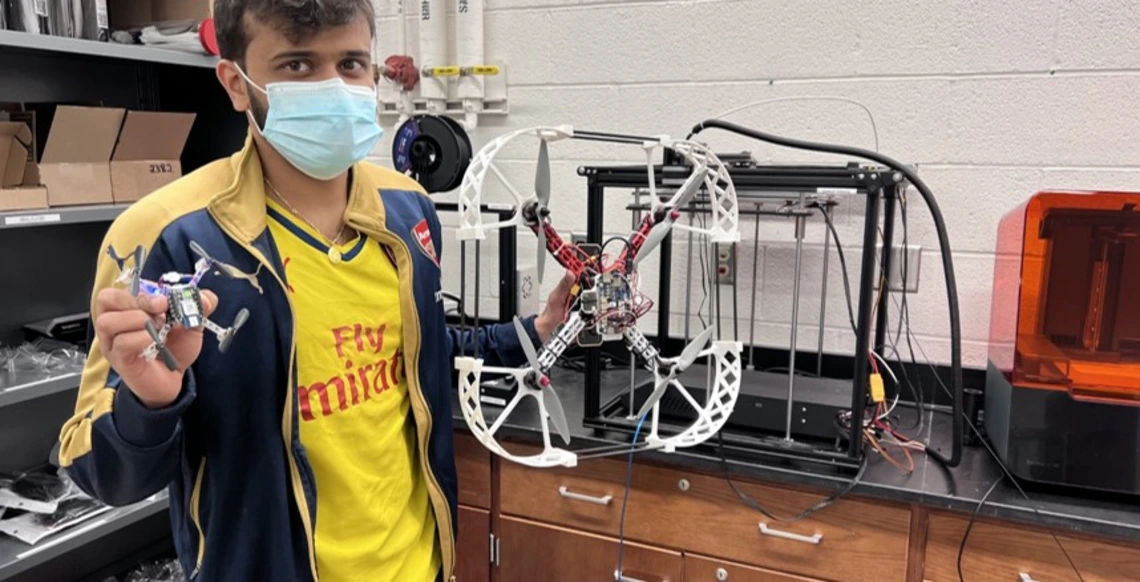